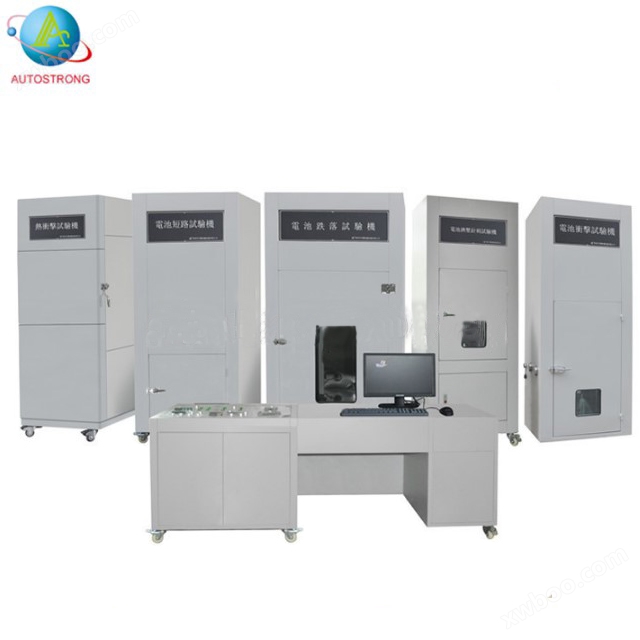
Integral Battery Safety Control System
Description:Integral Battery safety control system is mainly applied to test battery performances when battery in hazard environment or damaged externally by electrical test and mechanical test, which is introduced by research institute and battery manufacturers
Model:AUTO-BSCS
Manufacturer:
Update time:2024-05-09
Visits:110
Available to customize by increasing or reducing testing projects in compliance with customers’
demands or different standards;
One Control cabinet to control all testing systems;
Compartment design can be available to make all equipment in same height with the advantage
to reduce to time , cost and mobile to move & upgrade test equipment.
Model | AUTO-BSCS |
Items | Test Method |
Crush |
The test battery is placed between two planers and approximate 13KN crush force can be performed through hydraulic arm with an 32 mm diameter piston or bench clamp; The crush remains till hydraulic pressure reading data up to 17Mpa. Once crush force reached and system will release automatically; |
Nail Penetrate | Battery specimen is placed and fixed in a planner, nail penetration speed at 10mm ~ 40mm remains to setting time and pull out steel nail automatically to complete test. |
Impact |
Battery specimen is placed on a planar, a bar with its diameter is placed on the center of the battery specimen, a weight at 9.1kg drop onto battery specimen from height of 610mm. Battery crush is placed onto shock bench, a weight drop free from a height of 100mm to hit the fixed battery (the max. Area side is vertical to bench) |
Low Air Pressure | Battery is placed into vacuum oven after recharged. After sealed, reduce air pressure less than and equal to 11.6Kpa (altitude at 15240m) and remain 6hours for testing. |
Free Drop |
Battery specimen drop free from a height of 100mm onto the concrete. Each side of battery for drop test, total 6 tests |
Short Circuit |
In a condition of 55±5℃, battery is connected to thermal coupling (contact of thermal coupling is fixed onto the center of the max. area side of battery) and placed in vent cabinet and make circuit-circuit for positive pole and negative pole with short-circuit of 80mΩ±20mΩ, any condition listed below will stop test: A.. Battery temperature drop to 20% of peak value; B.Short-circuit time reaches 24 hours |
Thermal Shock | Battery is placed in hot oven with temperature rises at a rate of(5±2)℃/min to (150±2)℃ and remain 30 min. |
Burning |
Battery is placed in a hole with its diameter 4 inches and a cover place onto the plane bench. The cover plate is made of 20 holes per inch steel mesh or steel wire at 0.017 inch (0.43mm); a mesh screen with 8 sides at size of 2 inches(610mm width) and 1 inch (305mm height) is surrounded; The metal mesh is made of 16-18 wires per inch with wire diameter of 0.010 inch (0.25mm) metal wire. Specimens is placed onto metal mesh , cover on the central hole and heat to explode or damage. |
It is complied with standards from UL, IEC, UN, QC, YD etc, and designed with remote test
method to perform testing projects.
Fill out the form